Advanced risk control measures for dangerous machinery operations
Operating dangerous machinery presents significant risks, making it essential to implement advanced control measures that go beyond standard ...
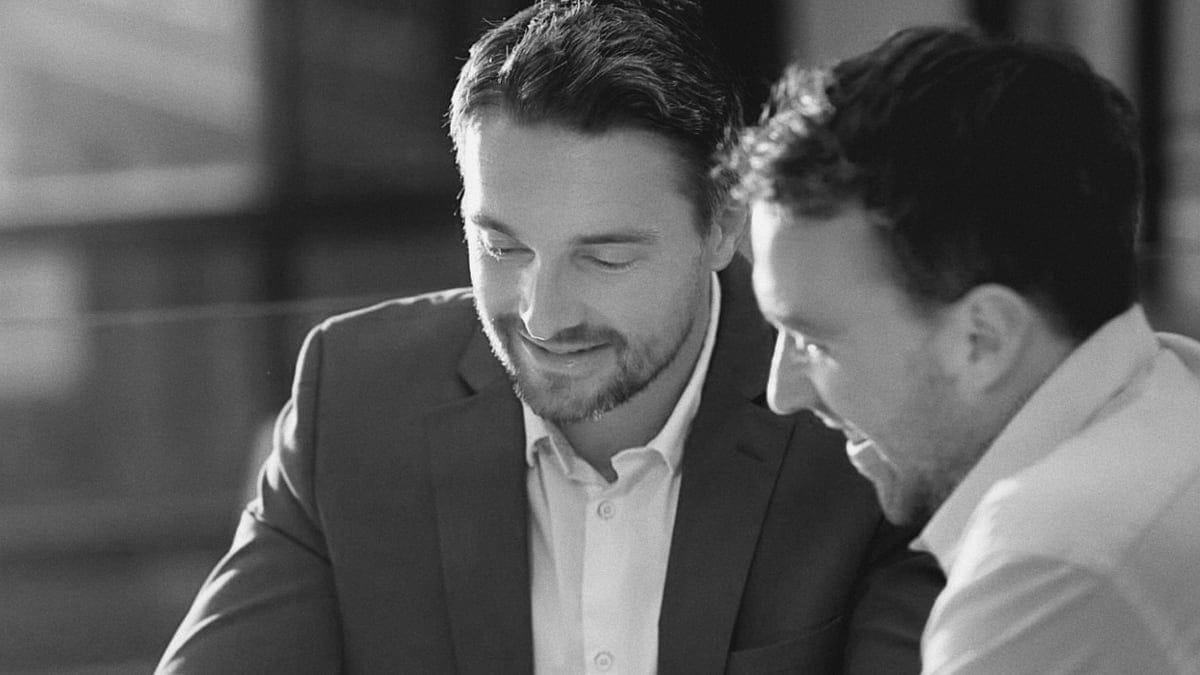
Operating dangerous machinery presents significant risks, making it essential to implement advanced control measures that go beyond standard protocols.
While most workplaces adhere to basic safety procedures, a deeper understanding of risk management can lead to better protection for workers, reduced downtime, and compliance with stringent Australian workplace safety regulations.
Understanding the full spectrum of risk
Traditional risk assessments focus on immediate hazards, but a more advanced approach considers a broader spectrum of risk factors.
Beyond the obvious mechanical dangers such as crushing, entanglement, and shearing, operators must account for human factors, environmental influences, and long-term exposure risks.
Human error plays a major role in workplace incidents. Fatigue, distractions, and cognitive overload can lead to misjudgments, increasing the likelihood of accidents.
Addressing these issues requires a combination of engineering controls, administrative policies, and worker training tailored to the complexities of each specific machine.
Environmental factors, such as temperature extremes, noise levels, and lighting conditions, also affect the likelihood of incidents.
A truly comprehensive risk control strategy integrates these elements into a dynamic safety framework.
Engineering controls that go beyond the basics
Basic engineering controls such as emergency stop buttons and fixed guarding are standard in most workplaces.
However, advanced risk control measures incorporate more sophisticated solutions, including interlocked barriers, pressure-sensitive mats, and automatic shutdown systems.
Interlocking guards ensure that a machine cannot operate unless all safety barriers are properly in place. This prevents accidental exposure to dangerous moving parts.
Advanced sensors and artificial intelligence-based monitoring systems can detect unusual worker movements or unsafe proximity, triggering an automatic shutdown before an incident occurs.
Another crucial advancement is adaptive machine learning technology, which analyses operational patterns and predicts potential failures before they happen.
Predictive maintenance not only prevents sudden malfunctions but also reduces the risk of catastrophic mechanical failures that could endanger workers.